初心者向けの静電気防止、静電気除電対策のガイドとして下記のポイントをメインに解説しています。
・静電気防止、静電気除電の原理、仕組み
・静電気防止、静電気除電の違い
・静電気防止、静電気除電グッツ
工場、現場等での静電気除去対策にご活用ください。(^_^;)
静電気防止、静電気除電とは
静電気による障害や事故は静電気の発生を抑えれば避けられるが,これは実際には困難であるため,発生した電荷を除去する“除電”が行われる。固体の内部や,液体,堆積した粉体などを除電するのは困難であるけれども,固体表面のような面を除電することはできる。
除電は,帯電電荷と逆極性の電荷を帯電部分に運び,電荷を中和して行う。逆極性の電荷を発生させるのに放射性同位元素を用いる方法、コロナ放電による方法がある。
除電器や除電バーは広く使われており,とくにプラスチック・シートなどを扱っている工場では,非常に多数の除電器が設置されている。ユーザーにとっても,除電器や除電バーを有効に投資効率よく使用するために,除電の基礎知識は有用である。
コロナ放電による除電方法
まず尖った針や細い線で生じるコロナ放電について述べる。コロナ放電は,イオン発生器として除電用だけでなくさまざまな静電気応用に使われているのでややくわしく説明しておこう。
図3.1は,直流電圧を印加した場合のコロナ放電の電流一電圧特性の例である。
電極はコロトロンで,直径60μmのタングステン線が張ってある。外側の接地缶電極の断面はコの字形で,その内寸の長辺は22mm,短辺は15mmで,長辺の1つが開口部であり,線は開口から5mm奥にある。本書で測定結果を示すコロトロンの缶の形状は,すべてこれと同じである。
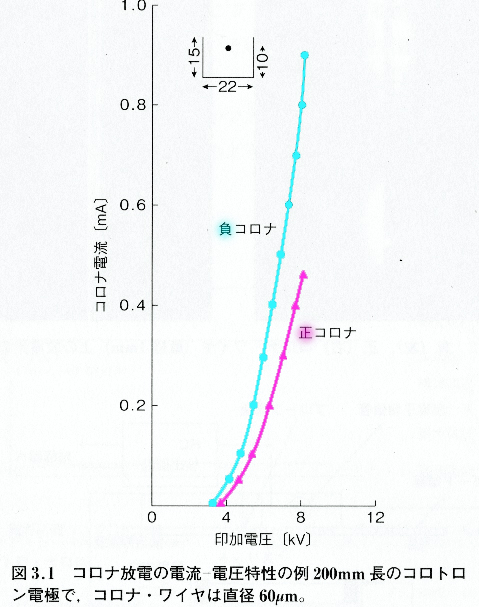
コロナ放電 電流ー電圧特性 画像出典先:静電気を科学する 高橋雄造 (著)
電圧Fをゼロから上げていきある電圧になると尖った針や細い線から設置電極へと電流Iが流れ始める。この電圧をコロナ開始電圧Viと名づける。さらに電圧を上げると電流は増大する。電流Iと電圧Vとの関係は,ほぼ次式で表される。
Aは電極の大きさ(針先端の曲率,線の径)や対向電極への距離などで決まる係数である。
I=A×(V-Vi)×V
要するに,コロナ電流Iは電圧Vの二次関数であり,ある電圧Viまではゼロでは立ち上がらないということである。図3.1は,有効長さが200mmの線の場合であり,電流は1mA以下である。線でなく針であれば,電流はずっと小さい。
ここで,尖った針や細い線に負の電圧をかける場合(負コロナ)と正の電圧をかける場合(正コロナ)との極性による違いに注目してほしい。コロナ開始電圧柘は負コロナの方が小さい。同じ電圧で比較すると,電流Iは負コロナの方が大きい。つまり,電荷供給能力は負コロナの方が優れている。コロナ放電を利用するのには高電圧電源が必要で,これは,大きさ,重量があり,高価であって,しかも安全に注意する必要がある。
高電圧電源を切り詰められるという意味では,負コロナの方が好ましい。正と負のどちらのコロナを使うにしても,大気中である限り(減圧するとRは低下する)数kVの高電圧電源が必要である。正コロナは電圧を上げると火花放電になりやすいのに対して負コロナは電圧の広い範囲で安定である。ふつうは,コロトロンにVの2倍程度の電圧を印加して使う。
しかし,負コロナには難点もある。そのひとつは,線電極上のコロナは均一でなく,局所的であることである。正コロナは,均一性が優れている。図3.2のコロナ放電光の写真から,これが明らかである。
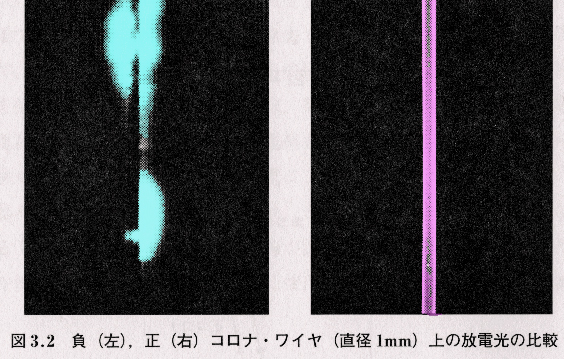
正負コロナ放電 比較 画像出典先:静電気を科学する 高橋雄造 (著)
コロナ放電はオソン発生を伴う。負コロナは正コロナよりもオゾン発生が多いので,これも難点である。
能動除電
コロナ放電電極に高電圧電源を接続し,発生する電荷で除電することを能動除電という。後述のように,高電圧電源を使わない場合を受動除電と呼ぶ。
電荷発生用につくったコロナ放電電極をコロトロン(corotron)と呼ぶ。図3.5は複写機用のコロトロンで断面がコの字形の金属缶の中に細いタングステン線を張ってある。線でコロナ放電が起きて電荷が生じ,この電荷は接地した金属缶へ流れるだけでなく,コの字の開口から流出するので,開口部の外側近くに物体を置くと,これに電荷が到達する。図のコロトロンのコロナ電流一電圧特性は,図3.1に示してある。コロナ開始電圧Kは3~4kVであり,6kV程度の直流電源と組み合わせて使う。
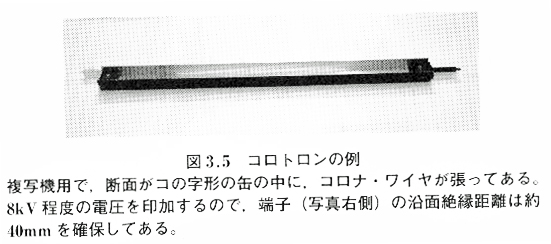
コロトロン 画像出典先:静電気を科学する 高橋雄造 (著)
能動除電では,図3.1のような電流一電圧曲線上の任意の電圧を選ぶことができるから,供給する電荷の極性も量も自由に設定できる。除電対象物体が移動するような場合(プラスチック・シートをローラーで搬送するなど)でも,電荷供給量を多くして対応できる。
極性に関しては,除電対象物の帯電とは反対の極性の直流電圧をコロナ電極に印加する。正電荷と負電荷の両方を供給し,しかもその比(イオンバランス)を変えられる機種もある。帯電の状態に応じて電荷供給を自動制御することもでき,そのようなシステムも商品化されている。
コロナ電極に交流を印加することもある。商用交流(50HZか60HZ)では,前項で述べたような正コロナと負コロナが半サイクルごとにくりかえされる。このような交流除電器では,正電荷と負電荷の両方を供給できる。コロナ放電で生じた正電荷は対象物の負帯電部分に,負電荷は正帯電部分に引き寄せられて,それぞれ帯電を中和する。
能動除電では高電圧電源を使うので,もしコロナ放電でなく火花放電が起きると,電源から相当のエネルギーが注入され,場合によっては着火・爆発のもととなる。交流高電圧を印加する除電器であれば,漏洩変圧器を使うとか,変圧器と除電電極との間にコンデンサを入れるとかの方法により,注入エネルギーを制限できる。交流除電器でも,イオンバランスを考慮した製品もある。
除電すべき物体の面には,実際には電荷が均一に分布しているのではなく,いわば濃淡があり,正帯電と負帯電の箇所が両方ある場合が多い。正帯電部分と負帯電部分がある場合は,交流除電器が有効であると考えられる。
能動除電では,帯電電荷と逆極性の電荷を供給して中和するにとどまらず,逆極性に帯電させてしまうことがある。プラスチック・シートを除電するとき,シートの裏側に接地金属板などがあるとこれが起きやすく,注意が必要である。接地導体を覆っているプラスチック・シートに対して直流除電器を使うと除電というよりも除電器の極性の電荷をシートに与える帯電装置となる。
除電効果からすれば除電対象物のなるべく近くにするのが望ましい。しかし,10mm程度まで近づけるのは実際には困難な場合がある。
そこで,空気流で電荷を送る送風式除電器がある。
コロナ放電ではイオンが移動するので,イオンが空気にぶつかり空気流を生じる。これをコロナ風と呼ぶ、コロナ風の流速は,数m/s程度である。
送風式除電器では,コロナ風よりも強い風でイオンを送る。例を図3.6と図3.7に示しておく。
図3.6は,フアンの風にのって電荷が飛んでくる(イオン風が飛んでくる)ようになっていて,この風を除電対象物にあてる。図3.7では,チューブでイオンの風を除電対象物近くまで送る。この例では,幅の広いシート状の対象物をローラで搬送しながら除電するために,イオンの風の吹き出しを対象物の幅と同じ長さの棒に分布させている。除電器にはこのほかいろいろな種類や形状のものがあり,対象物などによって選んで使う。
関連記事:イオナイザーの正しい選び方、使い方
帯電物体の帯電電荷と帯電電位
能動除電の次に受動除電を述べる順序であるが,その前に帯電物体の帯電電荷と帯電電位について説明しておく必要がある。
図3.8のように,接地板の上に絶縁板があって,その上面が帯電しているものとする。帯電電荷が単位面積あたりqであるとする。絶縁板上面の対地静電容量が単位面積あたりcであると,絶縁板上面の帯電電位はq=c×V則から
V=q/c
である。ここでCは絶縁板(比誘電率ε,厚さt)をはさんだ平行板コンデンサを想定して
c=εo×εr/t
である。εoは真空の誘電率である。
実際に帯電電位を測定するときには,図3.8(a)のように測定器を上方から近づける。測定器のヘッドや筐体は接地物体と同じことであるから,これによる対地静電容量の増加分に応じて電位測定器直下の絶縁板の電位は低下する。この意味では電位測定器は測定対象物から距離を置く方が良いのだが,測定感度などからすれば近づけた方が良い。市販の電位測定器では,この距離が指定されていたり,所定の距離の位置になると音を発して合図するようになっていたりする。
帯電電荷は,絶縁板上に均一に分布しているとは限らない。この分布をくわしく調べるには,電位測定器のセンサを小型化して,対象物の直近に置く必要がある。分布を測定する分解能は,だいたいのところ,センサー対象物間の距離に等しい。たとえば,この距離が10mmであれば,10mmよりもずっと細かい模様の測定はできない。
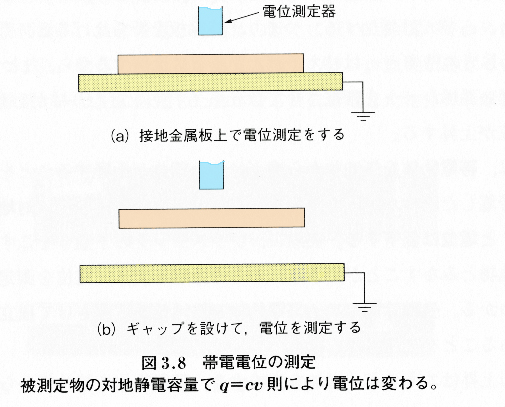
帯電電位の測定 画像出典先:静電気を科学する 高橋雄造 (著)
さて,図3.8(b)のように,帯電した絶縁板を持ち上げたらどうなるであろうか。
電荷がリークして逃げたりはしないと仮定する。絶縁板上面の対地静電容量(単位面積あたり)C’は空気ギャップの静電容量(単位面積あたり)Cdが直列Cに入るので
C’=1(1/C+1/Cd)
となって低下する。空気ギャップがdであるとすると
Cd=εo/d
である。このときの絶縁板上面の帯電電位v’は
v’=q/C’=q(1/C+1/Cd)=q/C+q/Cd=q/c(1+C/Cd)
となり,C/Cd倍だけ増加する。つまり,絶縁板を持ち上げると,帯電電位は上昇する。上昇分の倍率C/Cdは持ち上げた距離dこ比例するから,たとえば厚さ1mm以下の薄い絶縁シートを帯電させて数mmも持ち上げたりはがしたりすると,急激に電位が上昇する。
逆に,帯電した物体があったとして,これが接地物に近づく(対地静電容量が増加する)と電位は低下する。実際に,プラスチックの下敷きをこすって帯電させ,机(接地物とみなすことができる)からの距離を変えて電位を測定すると,これがよくわかる。受動除電では,帯電物体を接地物から遠ざけて孤立させることが肝要であること。
電位の上昇はエネルギー増加を意味する。帯電物体を接地板から持ち上げたりはがしたりするときには力学的仕事をするので,エネルギー増加になるのである。
帯電したシートが(クーロンカで)接地板にへばりついてはがれにくいというのは,よく経験することである。
受動除電と除電ブラシ
受動除電では,高電圧電源を使わずに,除電する対象物に“除電ブラシ”を近づけて置く。除電ブラシは,図3.9のように塗装用の刷毛の幅を広くしたような(数百mm)形状をしている。除電ブラシを自己放電式除電器と呼ぶこともある。
除電ブラシの毛には細い金属線や力-ボン繊維を使用し,接地して使う。帯電した物体は,接地に対して相当に高い電位になる。プラスチックの下敷きをこすっただけでも数kV~数十kVになる。数kV~数十kVの電圧がコロナ放電を発生させるのに十分であることは,図3.1の電圧と比較してもわかる。
帯電した物体に接地した除電ブラシを近づけると,この電位により除電ブラシの毛の先からコロナ放電が起きる。帯電物体の極性が正ならば,接地除電バーは帯電物体に対して相対的に負であるから,除電ブラシのコロナ放電は負コロナである。同様に,負に帯電した物体の近くに置いた除電ブラシからは正コロナが起きる。つまり,物体の帯電を中和する極性のコロナ放電が起きるのである。このように,除電ブラシは正に帯電した物体でも負に帯電した物体でも除電できるから,便利な存在である。
除電ブラシ自体は高電圧電源を持たず除電対象物の電位を利用するので,これによる除電方法を受動除電と呼ぶ。除電ブラシは安価であり,設置は簡単で,高価かつ安全への配慮の必要な高電圧電源を使用しない。 しかし,除電ブラシが有効であるためには条件がある。以下,これを述べよう。
除電ブラシが有効であるための条件
図3.10は,除電ブラシの動作範囲の電流一電圧特性の説明である。除電ブラシのコロナ放電は,帯電物体の電位付近で始まると考えてよい(正確には,除電ブラシ自体も接地物体であるから,これを帯電物体に近づけた分だけ帯電面の対地静電容量が増大して,帯電電位は低下する)。このときの電荷供給能力は,図3.10の太線のIの値である。帯電物体の電位は対地静電容量で変化するから,除電対象物をなるべく接地物体から遠ざけて(近接物体のない孤立した状態で),対地静電容量小・帯電電位大にして除電ブラシを設置するのが良い。
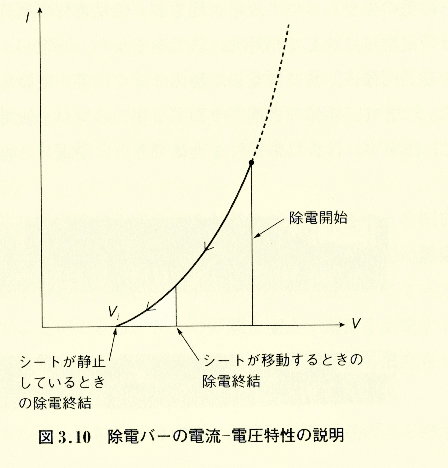
除電ブラスの電流 電圧特性 画像出典先:静電気を科学する 高橋雄造 (著)
図3.11は,数種類の除電ブラシからのコロナ開始電圧を実測した結果である。除電ブラシが負である(除電対象物が正である)方が,極性がこれと逆である場合よりもコロナ開始電圧は低い。
すなわち除電ブラシは,正に帯電した物体を除電する方が,負に帯電した物体を除電するよりも,有効にはたらく(他の条件が同じであれば)。除電対象物と除電ブラシとの距離が小さい方が,コロナ開始電圧柘は低い。しかし,この距離を5mm以下にしてもViは1kV前後である。したがって,除電ブラシでは約1kV以下の除電はできない。除電でブラシ除電しても,約1kVの電位が残るのである。
以上述べた除電バーの動作範囲は,除電対象物と除電バーの運動がない場合である。プラスチック・シートをローラで搬送するときなどの場合,帯電物体(プラスチック・シート)が相当の高速で動く。コロナ放電で生じた電荷は電気力線に沿って動いて帯電面に到達する(その所要時間は電界強度とイオンの移動度で決まる)のであるが,帯電物体が高速で移動していると除電が間に合わない。こういう場合は,除電は図のVi以前で停止してしまう。このとき,除電したつもりでもViよりも高い電位が残るのである。
除電バーにはコロナ開始電圧Viが低いことが望まれる。そのため,除電バーの毛の先が鋭く尖った針状になるようにワイヤにはつとめて細い線を使い,その毛の先端の電界が非常に高くなるようにする。市販の除電バーには,直径約20μmのカーボン繊維を多数あわせて0.3mm程度の太さにして使用している例がある。
しかし,いくら細い毛を使っても,毛が多数密集していると,毛先の電界は低下する。葉が尖った針葉樹であっても,樹のシルエット(包絡線)は滑らかな線になってしまうのと同じである。
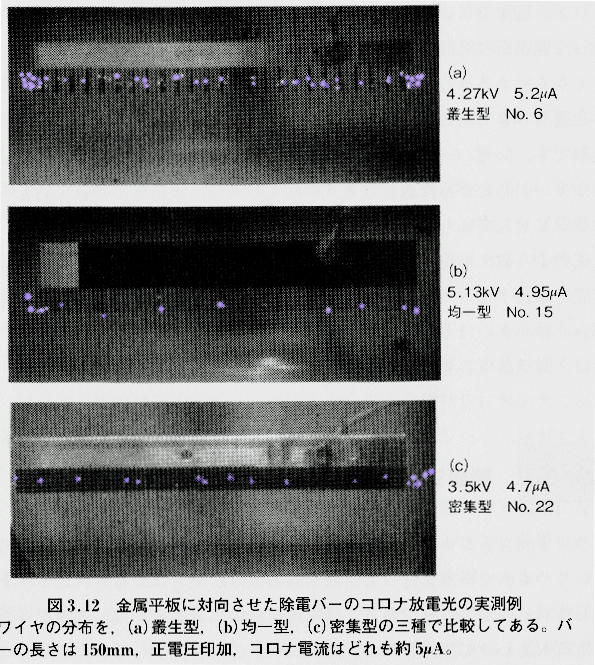
除電ブラシのコロナ放電光
図3.12は,市販の除電バーを接地金属(平板)と対向させたときに起きるコロナ放電光を,超高感度カメラ(イメージインテンシファイヤを前置したカメラ)で記録した結果である。ワイヤの材質は放電特性に事実上影響しないが,図の例ではステンレスまたはカーボンである。図を見ると,バーのワイヤが均一に分布している均一型(b)よりも,ワイヤの束相互に間隔がある叢生型(a)の方が光点が多い。
叢生型の場合,光点はワイヤ長さの中途に多いことから,乱れてはみ出した“おくれ毛”の先から放電していることがわかる。同様に,非常に多数のワイヤを植えた密集型(c)で払放電は“おくれ毛”から生じる。またバーの端部で光点が多いことからも,ワイヤが密集していると電界強度が小さくなって放電が起きにくくなり,除電しないことがわかる。
これらの結果から,①“おくれ毛”がない理想の場合は,均一型が良く,ワイヤはまばらな方が良い,②実際には“おくれ毛”があるので叢生型が良い,と結論される。密集型はメリットがない。市販の除電バーには,材料に紙や布やゴムを使って鋸歯形にしたり,ワイヤ長さを大きくしたり(ワイヤは長くすると折れやすくなるであろう),さまざまなバラエティがあるが,これらには特別な利点はないと言うべきである。
実験でも,除電バーに負電圧を印加した方が低い電圧でも正電圧印加に比べて光点が多い。 したがって自己放電式の除電バーは,正帯電の物体に対しては負帯電の物体に対してよりも有効に作用することがわかる。
上述のように,除電バーには対地静電容量が小さいことが求められる。それゆえ,毛を支持するワイヤホルダーは金属でなくプラスチックを用いて,寸法(幅と厚み)は小さいほど好ましい。非常に多数の毛や,数十mm以上の長い毛を使うのは,対地静電容量を増やすことになるので,避けるべきであろう。
絶縁性シートの両面帯電と除電
プラスチック・シートなどの絶縁性シートでは,両面に帯電している場合がある。いくつものローラを通って何回も巻き取りと巻きほぐしされたシート面は,帯電しているのがふつうである。帯電電位計による測定では,表側だけでなく裏側の電荷もあわせて測定される。薄いシートの場合,少し離れたところ(距離はシート厚さの数十倍以上)に設置した電位計で測定されるのは,両面の帯電電荷の代数和で決まる電位である。 もし,表裏の帯電電荷が正負反対極性で絶対値が等しいならばにのような状態を電気二重層とい引,電位計で測定してもほとんど帯電していないのと同じ測定値になる。
表裏逆極性に両面帯電したシートは,“電気力線が外に出ない”ので,電位計や除電バーにとって“帯電していないように見える”のである。
両面帯電したシートを除電するのは,容易ではない。同極性に両面帯電している場合,除電器(とくに能動除電器)は表だけでなく裏面の電荷まで除電するように電荷を供給しようとする。除電器から送られる電荷はシートを貫通して通り抜けることはできないから,シートの表に堆積する。こうして,表は過除電されはじめの帯電電荷とは逆の極性の電荷が堆積する。
シート裏側の帯電電荷はそのまま残る。結局,電気二重層が形成される。
表裏逆極性に両面帯電している場合は,上述のようなわけで,単に除電器をあてただけでは効果は非常に少ないと考えられる。
実際のシート面の帯電は,単一極性ではなく,帯電電荷密度も場所によって変化する。ちょうど,地図の上で場所によって標高差があり,海面より下のところもあって,海の中でも水深が場所によって異なるようなものである。こういう帯電物体を除電するのは,たやすいことではない。
以上に示した基本の考え方を基礎にして工夫すれば,状況に応じた改善法が見つかるであろう。
除電にはある程度の時間がかかる。除電器からの電荷供給量は無限大ではないから,帯電を中和するには時間がかかる。実際には,長尺シートを除電するときのように対象物が移動することが多い。移動速度が速い場合は,除電不十分になるし,逆の場合は過除電になって対象物を反対極性に帯電させる結果になる。
それゆえ,除電の実施にあたっては,実験的に決める必要がある。除電後の対象物の帯電状態を測定監視して除電器を制御すればよいが,大掛かりなシステムになり,設置スペースからも,費用の点でも実行できない場合が多い。除電はこのように,簡単で容易なことではなく,研究すべき事項が残っている。
湿度による除電
雰囲気の湿度を上げるのが静電気問題を生じにくくする方法である。静電気による障害や事故は冬に起きやすく,湿度の高い夏場には起きにくい。しかし,エアコンが普及した今日,冬には室内の相対湿度が40%以下になるのもふっうである。
シートやフィルムを扱う工場では,冬になって静電気問題で困ると,よく床に水を撒くのだという。簡単明瞭で安上がりな方法である、湿度を上げてリークを増すのは,表・裏とか,過除電とかいった面倒なことを考えなくてすむので,合理的である。
湿度が高くなくても,リークを増すことができれば除電になる。表面に界面活性剤を塗布して水分の作用によりリークを増すことは,第2章で述べた。導電性ないし半導電性の材料を塗布すれば,表面の水分の有無にかかわらず除電効果が大きくなる。
表面の導電性を増すだけでなく,材料のバルク(体積)の導電性を大きくすることも効果がある。カーボンブラックなどを練り込むのは,よく行われている。作業服とか繊維製品の場合,糸に一部分,金属線や導電性のものを使う場合がある。
材料の選択
接触・摩擦によって発生する電荷の量(時には極性も)は,接触し合う物体の材料を選ぶことによって変えることができる。これには,以下のようなことを参考にするとよい。
帯電列の利用
ある材料の帯電を問題にするとき,これと接触あるいは摩擦する材料として,帯電列上でできるだけ接近した位置にあるものを選ぶ。こうすると発生する電荷は,帯電列上で離れた位置にある材料同士の組み合わせの帯電上りも遙かに少なくなるはずである。例えば,ポリエチレンフィルムがナイロンと摩擦されるときよりも,ポリプロピレンと摩擦されるとき方が帯電量はずっと少なくなる(下図)。
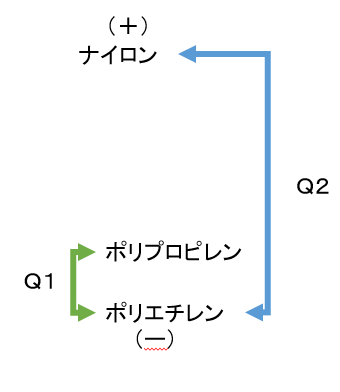
図 帯電列の利用
ポリエチレンはナイロンと摩擦されるよりも,帯電列上で近い位置にあるポリプロピレンと摩擦されるときの方が電荷発生量が少ない(Q1 < Q2)
同一物質どうしであれば,原則的には電荷は発生しない。
使用している材料は種々の特性を考慮して選択されているわけであるから,帯電傾向だけを考えて他の材料に変更するようなことができない場合が多い。そこで,一部分だけ材料を変更して,発生する電荷を逆極性の発生電荷で中和する方法も用いられることがある。例えば,パイプで流送される粉体の帯電を軽減するために,パイプ材料を部分的に逆極性帯電を起こすような材料に入れ替える。このように帯電列を利用して材料を選ぶことは価値のある対策である。
しかし実際問題として,少なくともこの方法には二つの問題点が存在する。第1は,公表されている帯電列のデータが少なく,しかも新しいデータがないことである。したがって,帯電を少なくできる材料の組み合わせを選択するためには,過去に公表された帯電列を参考にしながら,自分で種々の材料を選んでテストして見る必要がある。ある材料について帯電のしやすさをテストすることは意外に難しい。
この材料のテストでは正確な接触あるいは摩擦帯電のテスト装置を作るよりも,実際に稼働している装置で今使用されている材料を別の材料に交換して見てその効果を判定することが,結局は一番よい方法である。しかし,これが容易にできない場合,あるいはもっと汎用性のある評価結果を得たい場合には,別の評価法が必要になる。
問題点の第2は,材料の帯電傾向がその表面の汚れや使用履歴によって変化することである。材料を交換した直後は予定通りの帯電状態になったとしてもしばらく使用しているうちに帯電状態が変わってしまうことがある。また,吸湿性の高い材料では,湿度による帯電特性の変動かある。表面の幾何学的な模様も帯電特性に影響する場合かある。そこで,材料のテストはこれらのことも考慮して行う必要がある。
電気的性質
一般に絶縁性の高い材料ほど帯電しやすいと考えられている。これは多くの場合、正しいと言えるが,条件によっては正しくないことがある。
同じ場所に繰り返し他の物体が接触する場合では,電荷は接触回数に対して増加し,やがて飽和する傾向を示す。このとき,各回の接触が全く正確に同じ接触点で行われているとすれば, 各接触点ごとに電荷が増加して行くためには,前の接触で発生した電荷が分離中に接触点から移動して,次の接触までの間に接触点の電荷密度が減少している必要がある。
帯電する物体が完全な絶縁物では,この電荷の移動は原理的に起こらないことになる。実際の接触・摩擦が繰り返される場合には,いつも厳密に同じ場所で接触が起こるようなことは希で,少しずつ違った場所で接触している。そのため,繰り返し接触・摩擦による帯電量は,新たに接触される場所で発生する電荷によって増加して行く部分が多いと思われる。
しかし,これと同時に分離中の電荷の接触点からの移動が,長く続く電荷の増加現象を起こしている。そのため,多少電気伝導性があって,表面に発生した電荷が分離中に移動できるような材料ではなかなか帯電量が飽和せず,接触や摩擦が繰り返されている間,いつまでも増加してゆく現象が観察される。
この現象によって,電気伝導性の見地からも材料の選択を考えなければならないことが理解される。すなわち,接触・摩擦が繰り返し行われる状態では,絶縁体ではあっても電気伝導性がいくらか高い材料を使うことは好ましくない。この電気伝導性の程度を一般的な意味で定量的にいうことは難しいが,多少電荷が漏洩するような,絶縁体としてはあまり良質ではない物質で,むしろ帯電量が多くなる傾向にある。半導体や導体では電気伝導性が高すぎて,電荷は速やかに漏洩し帯電レベルがすぐゼロになってしまうことはいうまでもない。
表面の状態と材料の硬さ
接触、摩擦によって電荷が発生する現象では,接触面積が帯電量を決める重要な要因になる。この接触面積は,接触界面を挟んで電荷担体が移動できるような密接な接触状態にある面積のことーすなわち有効接触面積のことで,これには接触部分の表面の粗さや接触荷重が関係することは無論であるが,接触する物体の柔らかさにも大きく依存する。
材料表面はざらざらしているよりも鏡面に近いスムーズな面の方が接触帯電での帯電量は多くなる傾向にある。また,柔らかい材料では固い材料に比べて同じ荷重に対して有効接触面積が大きくなるから,帯電量も多くなりがちである。
以上のことを考慮すると,接触帯電量を少なくする目的では,粗いざらざらした面を持ち,硬度が高くてしかも帯電列上で接近した位置にある材料が望ましいことになる。
接触・摩擦の帯電条件
物体どうしが接触・摩擦で帯電する場合,その帯電量は接触・摩擦の条件によって当然変化する。電荷の発生量を低減させるためには,まず接触・摩擦の頻度を減らすことを検討すべきである。
これには,工程を見直し,できるかぎり他の物体との接触回数を減らすようにすることを考えるべきである。また,根本的に接触を避ける方法を検討することも必要で,特殊な例では,フィルム状の物体がローラと摩擦する部分を無くすために,空気流を噴射するスリットを設け,フィルムを浮き上がらせてしまう方法もある。
次に接触・摩擦の条件を変えることができるか否かを検討する必要がおる。接触・摩擦帯電は,接触圧,接触後の分離の速さ,摩擦速度などによって変化し,これらの値が大きくなると一般に帯電量が多くなる。
接触している二つの物体間に加わる加重が増えると,材料表面の変形量が多くなり有効接触面積が増加する。その結果,帯電量が増大することになる。
物体どうしを摩擦するとき,摩擦をゆっくり行うより速く行う方が一般に帯電量が多い。これには幾つかの原因が考えられる。
まず,同じ部分を繰り返し摩擦するときは,摩擦速度が早いと単位時間当たりの摩擦回数が増えるから,電荷の漏洩の影響が小さくなる結果,帯電量の増加が速くなる。摩擦する物体どうしの特定の接触点での接触時間は摩擦速度が速いほど短くなるが,接触時の帯電に必要な時間は極めて短いから,この点での差はほとんど無いと考えられる。
次に,分離速度の問題がある。一般に接触したあとで分離する際に電荷の逆流や放電による再分布が起こるわけであるが,この現象にも摩擦速度が影響するものと思われる。摩擦速度が速いと分離速度も速いためである。分離時の電荷の逆流はトンネル効果であるが,トンネル効果そのものは分離速度にほとんど影響されない。しかし,分離時に電荷が表面の突起部分に移動してからトンネル効果が起こるような場合は移動に時間がかかるから,最終的な帯電量に分離速度が影響するものと思われる。
お互いに摩擦し合った表面が分離するとき,多くの場合,静電気放電が発生することは何度か述べた。放電現象はトンネル現象に比べてはるかに遅い現象であって,分離速度が速いと放電によって減衰する電荷量も減少すると考えられる。
摩擦速度がどのような機構で最終的な帯電量に影響するかということについては,現在のところ上で述べた定性的な議論ができる程度で,あまりはっきりしていない。しかし,現実問題としては,例えば高分子の板を布で摩擦する際など,ある程度速く摩擦し,また特に摩擦を終わらせるための動作として布を素早く引き離すと,帯電量が多くなるのが普通である。
電荷の漏洩と帯電量
物体が連続して摩擦されるときなど,帯電の原因が継続する場合には,電荷が増加し、やがて飽和する。この飽和値はこれまで述べてきた電荷発生のさまざまな条件によって異なるが,もう一つ材料あるいは雰囲気を通しての電荷の漏洩が大きく影響する。
漏洩しやすい材料では,電荷が発生している間に常に電荷の漏洩が起こっているから,帯電原因が継続しているとき,帯電量の増加が緩慢で,しかも飽和値が小さくなる。帯電原因が除かれるとすぐ電荷は減衰し,なくなってしまう。
通常の高分子材料では,数分や数時間の程度ではほとんど電荷の減衰が起こらず,見ている間に減衰するような材料は,後述する特殊な処理を施さないと得られない。
接 地
金属などの導電性材料が帯電しているとき,これを接地する(アースする)と電荷は瞬間的に大地に流れ失われる。導体が大地から絶縁されて帯電している場合は,エネルギーの大きい静電気放電が発生する可能性があり,極めて危険であることもあって,導体は全て接地することが常識になっている。
接地は,第一種(高電圧用または避雷器用,接地抵抗10Ω以下),第二種(高圧または特別高圧電路と低圧電路を結合する変圧器の低圧側中性点, 150/IΩ以下,Iは高圧側の1線地絡電流),第三種(300 V 以下の低圧用, 100 Ω 以下),特別第三種(30Vを越える低圧用,10Ω以下)に分かれており,接地線の太さと接地工事方法が指定されている。しかし,静電荷を漏洩させる目的であれば,どのタイプでも問題はない。
接地抵抗をR[Ω],金属機器類の静電容量をC[F]とすると,電荷の減衰の時定数τ= RCで表される。Cの値は機器類の形状,大きさ,配置によって異なるが,仮にその値が1×10 -9F(1,000 pF, 人間の5倍前後)とすると,R=1[MΩ](Mは106を示す)でτ=1/1,000sになる。きちんと導線で接地した場合,通常こんなに大きい接地抵抗は考えられないが,この例から接地抵抗が10Ωでも100 Ω でも,電荷はほぼ瞬間に漏洩してしまうと考えてよいことが感覚としておわかりいただけよう。
下図に電荷の漏洩速度と接地抵抗の関係を示す。機械類の接地が忘れられることが最も危険で,またあるいは気がつかない間に接地部分が腐食して断線していたりして,十分な機能を発揮できない状態になっている場合があることを注意するべきである。機械などの金属類の接地は常に行っていなければならない。
帯電体に密着している金属体をいったん接地し,接地線を外すことは極めて危険である。帯電体に密着していなくても,ごく近くにある場合も同様である。接地によって金属体は誘導帯電で帯電する。接地線を外したあとで帯電体から離すと,金属体の電荷は回りに放電したり感電の原因になったり,さまざまな障害の原因となる。
絶縁体の場合はその一部を接地しても,電荷はほとんどというより,普通はまったく漏洩しない。絶縁体の一部に導体が密着していたり,あるいは絶縁体が導体容器の中に入っている場合には,当然その導体部分は接地しなければならない。絶縁体が多少の導電性を持っていれば,接地によって電荷が少しずつ失われることもある。
人体の電荷を逃がすには,人体は導体に近いから,接地が一番確実な方法である。それには,半導体生産工場などで使用されているリストチェーン(腕に導体のリングをはめ,このリングをチェーンなどの導体で接地端子と結ぶ)などを使用する方法がある。この方法は作業者が位置を変えないで作業できる場合にはよいが,歩き回る場合には向かない。
そこで帯電防止靴を使用する方法がある。この靴は,靴底が導電性になっていて,これを履いた人の電荷を逃がしてくれる。ただし,床が導電性でなければ効果が無いので,帯電防止靴と導電性床の組み合わせが必要となる。導電性床材料としては,プラスチックタイルの素材に導電性加工をしたものなど,各種の製品が市販されている。
湿度管理
静電気障害が発生しやすいのは,一般に夏より冬であることは誰もが経験するところである。これは冬の方が湿度が低いためであるが,湿度によって静電気障害の発生が影響を受ける二つの原因を述べる。
湿度が高くなれば,材料表面の吸着水分量が増すから,結果として表面の電気伝導性が向上する。そのため,特に吸湿性の高い材料では,湿度を上げることによって電荷漏洩の速度を早めることができる。材料によっては体積的な吸湿が起こり,材料全体の電気伝導性が向上するものもある。初期の静電気障害対策は湿度管理であった。
一方,帯電体表面の電荷の漏洩は,その材料の表面あるいは体積内を通る経路だけではないことが,最近の研究でわかってきた。これは,吸湿性が極端に悪いテフロン(ポリテトラフォルオロエチレンーPTFE)のような材料でも,夏と冬で帯電レベルに違いが出てくることからも推測される。
この現象は第2の漏洩経路,すなわち大気中への漏洩を考えないと説明がつかない。実験によれば,高湿度雰囲気中では,帯電体表面の電荷密度が高いと電荷は急速に大気中へ放出されるが,帯電レベルが低いとこの現象は目立だなくなる([下図]。したがって,電荷の気中漏洩では,電荷密度が高いとき電荷はある程度まで減衰するが,それ以後減衰速度が低下してしまい,一定レベルの電荷は残留してしまう。
この現象によっても,湿度を高く保てば材料の帯電レベルを障害の起こりにくい低いレベルに保つことが可能である。
材料の導電化
帯電する材料を導電化できれば,その材料の一端を接地することによって容易に電荷を除去することができるから,導電化は重要な帯電防止手法である。静電気の帯電を防止する目的では,金属のような伝導性は必要ない。導電化の方法としては,材料の表面を導電化する方法と,体積内部を導電化する方法に分かれる。
表面導電化
材料の表面のみの導電化は,その材料の機械的性質などを変えずに帯電防止できるから,最も広く利用されている方法である。この目的には帯電防止剤が多く使われている。
金属皮膜の形成
高分子材料表面に金属の薄膜を形成すれば,表面のみ導電化できる。この方法には,化学めっき,真空蒸着,スパッタリングなど,種々の方法がある。どの方法でも金属層の電気伝導性は極めて良いから,静電気を漏洩させるには十分すぎる特性を持つ。
導電性塗料
塗料に導電性材料の微粉を混入した導電性塗料がある。導電性材料としては,カーボンブラックや銀の粒子が用いられている。導電性塗料の塗装面は金属皮膜に比べると電気伝導性は劣るが,電荷を漏洩させる目的としては十分な特性を持っている。しかし,色とコスト,作業性などの問題点から静電気障害除去の目的にはあまり利用されてはいない。
表面の親水化
高分子材料の表面を何らかの処理によって,親水化する方法もある。たとえば,ポリエチレンを酸で処理する方法が試されたこともある。プラズマによる表面処理も有効であるといわれている。高分子材料のプラズマ処理は印刷適性の向上などを目的に以前から行われているが,処理によって親水性が増し,その結果水分の表面吸着が促進され,電荷漏洩が早くなる。しかし,プラズマ処理の結果は多くの場合永続性が悪く,処理後の時間経過に伴って処理前の状態に戻ってくる傾向を持っている。
体積的導電化
高分子材料の体積的な導電性を増すための最も一般的な方法は,導電性材料を高分子材料中へ混入することである。導電性材料としては,金属粉,カーボンブラック,カーボン繊維などが用いられる。粒子状の物体より繊維状の物体の方が比較的少ない混入量で導電性を増すことができるが,それでもかなりの量を混入しないとなかなか導電性が向上しない。これは,導電体どうしの接触が必要なためである。この方法では,帯電防止に必要な程度の導電性(多くの
場合10-8[S/m](S:ジーメンス,導電性の単位で1/Ω)程度の導電率と言われている)を得ることはむしろ難しく,必要以上の導電性になってしまうことが普通である。
導電性と強度の両方を増すためにウイスカ(髭のような単結晶)を混入した例もある。カーボン繊維が得られるようになってから,ウイスカのメリットはほとんど無くなったものと思われる。
導電性材料の必要な混入量を減らすためには,一定の大きさのペレット状の高分子材料を作り,その表面に導電性材料を付着させた後これを用いてホットプレスで成形する方法がある。
この方法では,成形された高分子材料が導電性の殼で構成されたセルに分かれ,各セルが接触し合っている構造になる。セル内の体積を導電化しなくとも全体としては導電性となり,良好な帯電防止性を得ることができる。導電性材料の必要量は,体積全体を導電化するよりもかな
り減らすことができる。
混入量の問題があるとしても,導電性材料を混入すれば確実に高分子材料を導電性にすることができる。この方法の欠点は,材料の不透明性と色の変化である。
帯電防止剤
電荷の漏洩を早めるために,界面活性剤の一種である帯電防止剤を利用する方法が古くから行われている。帯電防止剤の分子は親水基と親油基を持ち,高分子材料の表面に塗布すると親油基がその表面に向き,その反対の親水基が外部を向いて付着するため,帯電防止剤の分子層の数が奇数か偶数かによって表面の電気伝導性が変化することを示すデータもあったが,実際にはこれほど規則性があるかどうかはわからない。
ともかく高分子材料の表面が帯電防止剤で覆われると,親水基があるためこの帯電防止剤の層は空気中の水分を吸着し,その水分子の層がわずかな電気伝導性を持つため,電荷を速やかに漏洩させる。したがって,空気が極端に乾燥している状態では,その効能は低下することになる。
帯電防止剤を高分子材料に適用するには
① 高分子材料の表面に塗布する方法 ② 内部に練り込む方法がある。
塗布用(外部用)帯電防止剤は使用法が簡便であるが,表面を拭き取ったり洗浄したりすると,その効果が無くなってしまうことが欠点である。練り込み用(内部用帯電防止剤)では練り込まれた帯電防止剤は少しずつ表面に浸出(ブリートアウト)してきて,帯電防止作用をもつ。表面を洗浄しても,後からまたブリートアウトしてくるから,時間をおけば機能が回復する。しかし,樹脂によっては相溶性が悪く,なかなか均一に混ざってくれない場合もある。また樹脂との相溶性が良すぎてもブリートアウトしにくくなり,具合がわるい。
ブリートアウトの特性は温度の影響を受け,温度が高くなれば速くなる。またブリートアウトは高分子のガラス転移点以下の温度では起こりにくい。ブリートアウトするためには,帯電防止剤が高分子内部で拡散して行く必要があるが,分子鎖のミクロブラウン運動が凍結されている状態では拡散がほとんど起こらないからである。 ABSやPMMAなどの樹脂ではガラス転移点が室温より高いため,室温ではブリートアウトしにくい。これらの樹脂では,成形時にブリートアウトさせ,帯電防止性を持たせるようにしているが,その後表面の帯電防止剤がふき取られると,室温では帯電防止性が回復しにくい。
帯電防止剤が練り込まれた高分子の表面をコロナ放電処理やフレーム処理(炎による処理)すると,帯電防止効果が促進される場合がある。これは,これらの処理によって高分子表面の結晶が破壊され,帯電防止剤が表面に移行しやすくなることが原因であると考えられている。また,処理によって高分子表面に極性基が導入され,これが同じような極性基を持つ帯電防止剤を引きつけるためとも考えられている。高分子はコロナ放電などで処理されると,それ単独でも吸湿性が向上することから,この効果との相乗効果と見ることもできるかも知れない。
帯電防止剤は次の種類に分類されている。
① アニオン系帯電防止剤
② カチオン系帯電防止剤
③ 両性帯電防止剤
④ 非イオン系帯電防止剤
アニオン系帯電防止剤は,帯電防止効果は余り高くないが,表面の変色がなく,耐熱性にも優れている。
カチオン系帯電防止剤は帯電防止効果が高いが,これで処理した高分子を変色させる場合がある。
両性帯電防止剤は,カチオン系とともに帯電防止効果が高い。非イオン系帯電防止剤は,帯電防止効果は余り高くないが,高分子への溶解性をよくでき,練り混み用として使用されることが多い。下表に帯電防止剤の例を示す。
静電気トラブルと解析、対策資料 無料 ダウンロード
資料が無料でダウンロードできます。
自己学習、講座開催時にお役に立ててください。
グーグルスライド版 『製造現場における静電気トラブルと解析、対策』資料
Googleスライドから無料で『製造現場における静電気トラブルと解析、対策』についての資料がダウンロードできます。
スライドシェアー版 『製造現場における静電気トラブルと解析、対策』資料
スライドシェアから無料で『製造現場における静電気トラブルと解析、対策』についての資料がダウンロードできます、現場での静電気防止対策にお役に立ててください。
*さらに詳しい内容は下記の文献を参考、願います。
静電気除去 参考文献
トコトンやさしい静電気の本
実務で使う静電気対策の理論と実践: 事例で解説!
静電気を科学する
参考文献:
静電気の基礎と帯電防止技術 著者:村田雄司 日刊工業新聞社
たのしい静電気 著者:高柳 真
静電気トラブル Q&A 監修:田畠泰幸
図解 静電気管理入門 著者:二澤 正行 工業調査会
静電気がわかる本―原理から障害防止ノウハウまで 高橋 雄造 (著)
電気機器の静電気対策 (設計技術シリーズ) 水野 彰 (監修)